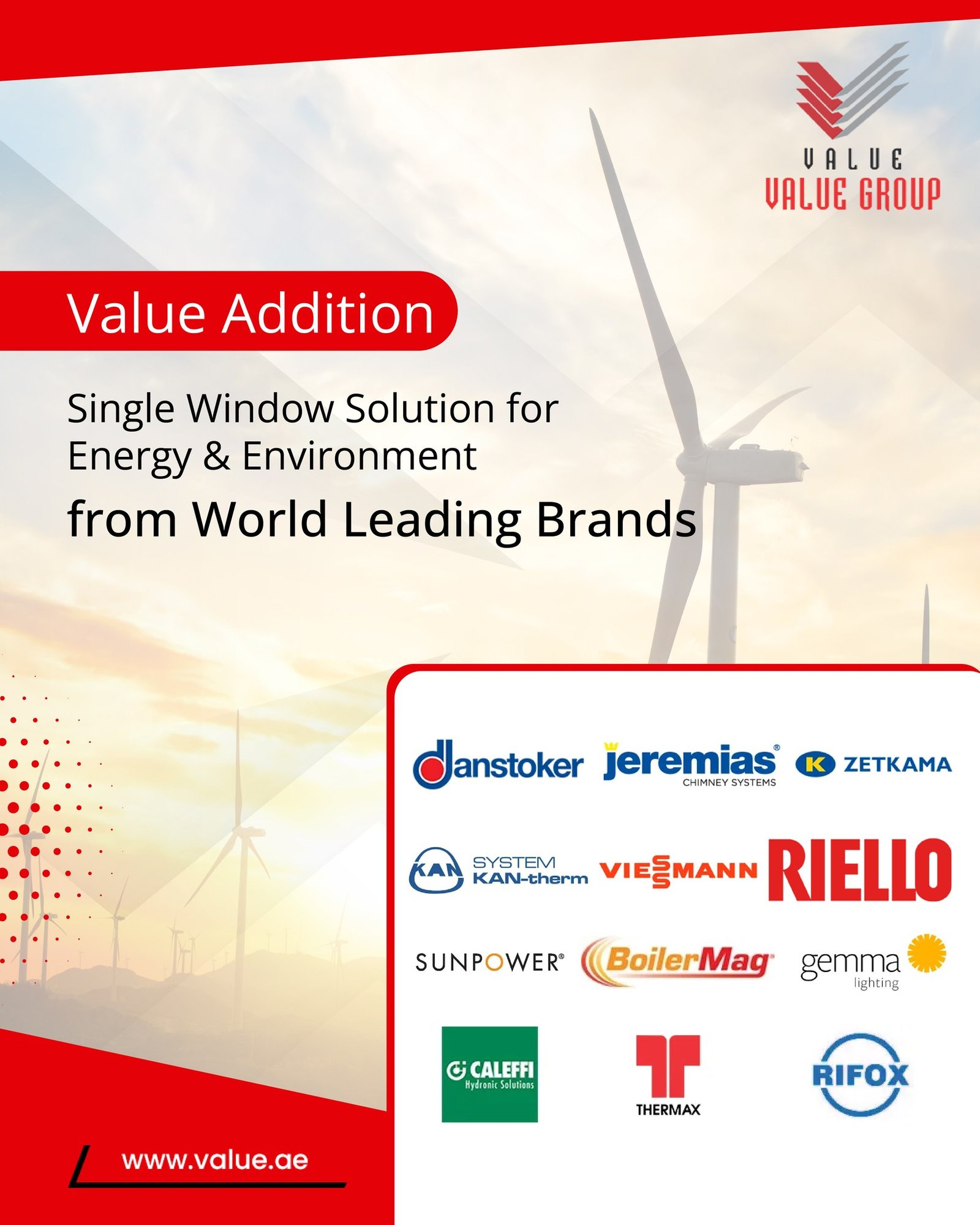
What Are the Types of Industrial Valves?
Industrial valves are essential components in various sectors, including oil and gas, petrochemicals, water treatment, and power generation. They regulate the flow of fluids—liquids, gases, or slurries—within a system or process. Selecting the appropriate valve type is crucial, as it depends on specific application requirements such as fluid type, pressure, temperature, and flow rate. Here, we explore some of the most commonly used industrial valves, their components, advantages, disadvantages, and typical applications.
Ball Valves
Ball valves are favored in industrial applications for their excellent sealing capabilities, versatility, and ease of operation.
Components:
- Body: The outer shell providing structural support and housing internal parts.
- Ball: A spherical closure element with a central bore that allows or blocks fluid flow when rotated.
- Stem: Connects to the ball and facilitates its rotation to open or close the valve, often linked to an actuator like a lever or motor.
- Seats: Located on either side of the ball, these create a tight seal when the valve is closed, typically made from materials like PTFE (Teflon).
- End Connections: Various types, including threaded, flanged, and welded, enable integration into different piping systems.
Types:
- Floating Ball Valve: The ball is not fixed to the stem and floats slightly downstream, pressed against the seat by fluid pressure to ensure a tight seal.
- Trunnion Mounted Ball Valve: The ball is supported by trunnions at the top and bottom, suitable for larger valves and high-pressure applications, offering greater stability and sealing.
Advantages:
- Quick quarter-turn operation (90 degrees) allows rapid opening or closing.
- Provides tight shut-off, minimizing leakage risks.
- Versatile for various applications, including corrosive and high-temperature environments.
- Simple design with fewer moving parts results in low maintenance.
- Allows bi-directional flow.
Disadvantages:
- Not ideal for precise flow control or throttling.
- Can cause moderate pressure drop, especially when partially open.
Applications:
- Water and wastewater treatment plants.
- Oil and gas pipelines and refineries.
- Chemical processing plants handling corrosive substances.
- Heating, ventilation, and air conditioning (HVAC) systems.
Gate Valves
Gate valves are primarily used to start or stop fluid flow, offering minimal flow restriction when fully open.
Components:
- Body: The main structure housing internal components.
- Gate (Disc): A flat or wedge-shaped barrier that moves perpendicular to the flow to block or allow passage.
- Stem: Connects the gate to the actuator (handwheel or motor) and moves it up or down.
- Seats: Provide sealing surfaces for the gate when closed.
- Bonnet: Covers the opening through which the stem passes and provides a seal.
Types:
- Rising Stem Gate Valve: The stem rises above the handwheel when the valve is opened, providing a visual indication of the valve's position.
- Non-Rising Stem Gate Valve: The stem does not move up or down; instead, the gate moves along the stem threads, suitable for limited vertical space.
Advantages:
- Offers minimal flow resistance when fully open.
- Provides a tight seal when fully closed.
- Suitable for bi-directional flow.
Disadvantages:
- Not suitable for throttling purposes.
- Slow operation due to multiple turns required to open or close.
- Occupies more space compared to other valve types.
Applications:
- Water supply systems.
- Oil and gas industries.
- Power plants.
- Mining operations.
Check Valves
Check valves, also known as non-return valves, allow fluid to flow in one direction only, preventing backflow.
Components:
- Body: Encases the internal parts.
- Disc or Ball: Moves to allow flow in the forward direction and blocks reverse flow.
- Seat: Provides a sealing surface for the disc or ball.
- Hinge or Spring: Returns the disc or ball to the closed position when forward flow decreases or reverses.
Types:
- Swing Check Valve: Uses a hinged disc that swings open with forward flow and closes against the seat when flow reverses.
- Lift Check Valve: Employs a disc that lifts off the seat with forward flow and returns to the seat when flow stops or reverses.
- Ball Check Valve: Utilizes a ball that moves away from the seat to allow flow and back onto the seat to block reverse flow.
Advantages:
- Prevents backflow, protecting equipment and processes.
- Operates automatically without manual intervention.
- Simple design with minimal maintenance requirements.
Disadvantages:
- Potential for water hammer due to sudden closure.
- Limited to specific applications based on design and materials.
Applications:
- Pumping systems to prevent backflow.